Main Street, City, State
Call Us For Free Consultation
Facebook | Twitter
Dknapp Fire Design PL
Interesting Projects
Sealy Perth Fabrication Facility Canning Vale Perth, WA

This project consists of a new warehouse/factory, fabrication facility, offices with a fire sprinkler system, external fire hydrant system and fire extinguishers (fire hose reels deleted as per the engineered fire design brief), all designed in accordance with the Factory Mutual Global Codes (FMG) for the expanded foam goods stored / manufactured as per FMG 2-8.
The facility has expanded stored foam, wooden bed framing and bedding materials, ground level stacking to maxheight of 3.0m, not stored in racking, all in accordance with FMG Codes. The facility has expanded stored foam, wooden bed framing and bedding materials, ground level stacking to maxheight of 3.0m,
not stored in racking, all in accordance with FMG Codes. The project has its own water supply from dual diesel fire pumps, drawing from fire water tanks in a grade 1 water supply configuration allowing for make water from the existing towns mains, serving both the fire sprinkler and fire hydrant system combined demands. To meet DFES (Fire Brigade) requirements, of 2 fire applicances attending, suitable parking has been provided at the main entrance, with fire brigade booster facilities either side, with water being drawn from the fire water tanks located approx 100 linear meters away via a storze hard suction connection, and boosting via 4 off DN65 boost hydrants, in each of the 2 cabinets. Calculations were carried out to ensure that the pressure losses in the suction piping from the tanks are minimal so the fire brigade applicance do not exceed their respective suction capabilities, and the boost line is sufficient size to minimal impact on the flows / pressures being provided by the fire applicances. At the time of posting this information on the web site, the project construction was only just starting, and no photos of the project are available, as the project proceeds then we will add photos to this page. We have included the site plan drawing for information.
Chandala Project (Tronox formally Tiewest) Muchea, WA Plant
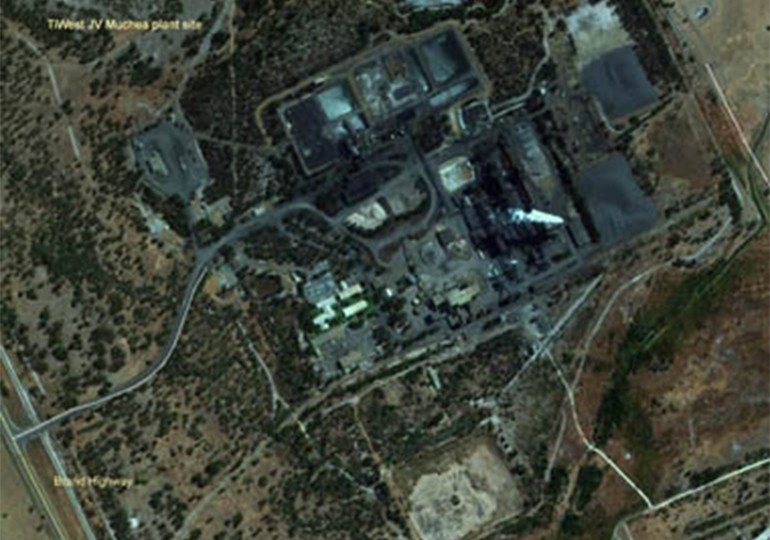
This project consists of a production facility, with various risks from simple sprinkler system to high hazards facilities and conveyors both horizontal and inclines vary up to approx. 20 degrees all must be compliant to Factory Mutual Global (FMG) codes.In 2012 & 2013 the fire pumps were upgrade to 2 off 100% capacity diesel driven pumps drawing from the existing onsite fire water tank (this tank is shared for fire protection and process facilities water needs). This is achieved by having the lower section of the water storage tank dedicated for fire protection ( the process water suction point is set mid level in the tanks, so the lower section is dedicated for fire use only). Using a guaranteed water make up supply from the existing bore water supply on site, that can supply the required
flows to achieve the requirements of FMG requirements. The 2 off new diesel fire pumps + an electric jockey pump complaint to FMG requirements, the jockey pump has capabilities of supply 1 off hydrant demand or process water requirements, The fire water tank is classified as a grade 3 water supply, with 2 dedicated 100% suction points at low level from the existing water storage tank. The new water supply connections had to be installed whilst the tank remained in operation for both fire and process water requirements. This was achieved by using specialized divers to weld in the new water supply feeds on the inside of the tank, and them making a hot tapping connection on the outside to ensure now water loss and allowing production to continue as normal.The fire water is currently distributed by a fire & process water ring main system throughout the plant, all fully calculated to ensure all the fire and process water needs can be achieved.The lasted upgrade was of the conveyor fire protection systems during the 2014 planned plant maintenance shutdown. To my knowledge this was completed.Adjacent is a picture of the sand mining operation approx 150 kms north of the Muche Refinery PlantTronox sand mining operation

Kinga Gardens, Perth WA

This project was an aged persons home, all complaint to Australian Standards requirements, with the roof structure similar to domestic housing (wooden roof structure), this present issues with piping routes through the ceiling voids, and to co-ordinate with the in-roof services (namely air conditioning / electrical / plumbing).In essence the fire main piping was run along the top of the ceiling rafters, ranges ran horizontally along the top of the roof rafters, using candle stick upright concealed space sprinkler heads aligned at roof level to follow the roof pitch as required by AS2118 requirementsKinga Gardens, Swan Village of Care Jarrah Rd Bentley WA
Bennett Springs Shopping Center, Perth WA
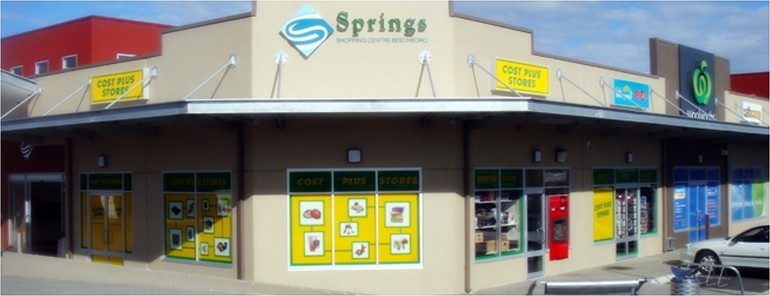
This project is a shopping centre complex, with a Woolworths Supermarket, and speciality shops, having both fire sprinkler protection and fire hydrant / hoes reels system all feed from the same water supply source.The water supply consisted of a grade 2 fire water tank arrangement (100% capacity), sized for both fire hydrant (4 hours operation) and fire sprinklers (high
hazards for 60 minutes operation). This was achieved by selecting the fire pump to supply the combined flow at the fire hydrant system pressure, and using Pressure Reducing Valves to reduce the pressure to the fire sprinkler system, to ensure no wastage of water & early depletion of the available water supplies (this is a common practice when dual type fire sprinkler/hydrant systems are involved).The makeup water / refill water was taken from the DN100 town's main, that could only supply limited flows, suitable for domestic requirements, and capable of refilling the fire water tanks in the prescribed time frames as specified by AS2118, but unable to provide any substantial make up flows.
Perth International Air Port upgrades, Perth WA
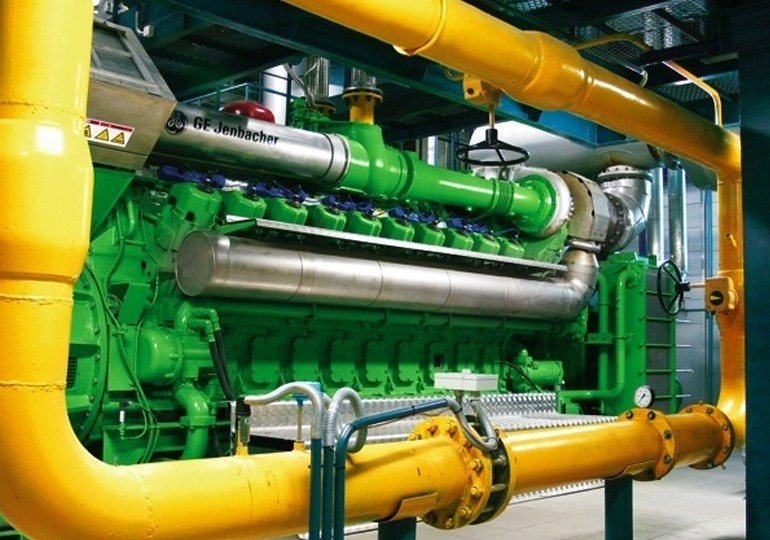
Co-Generation BuildingThis project included for the Co-Generation Building that houses emergency power supply generators for the airport complex, and fire pumps (1 off electric and 1 off diesel) + 2 off fire water break tanks (25 M3 each), with twin large diameter water supply feeds (grade 1 supply), capable of supply the total flow demand, but not the required pressures.Each fire water tank has 2 dedicated automatic 100% capacity infill valves (1 from each water supply) + low flow make up infill float valves to make up any minor flow requirements.The fire pumps are designed to provide the flow and pressure for combined underground ring main supply to the Perth International Airport Complex + Terminal
WA project, both fire hydrant (4 hours operation) and fire sprinklers (high hazards for 60 minutes operation). This was achieved by selecting the fire pump to supply the combined flow at the fire hydrant system pressure, and using Pressure Reducing Valves to reduce the pressure to the fire sprinkler system, located on the underside of the control valves, to ensure no wastage of water & early depletion of the available water supplies.
Terminals WA Project for Fly in-out workers
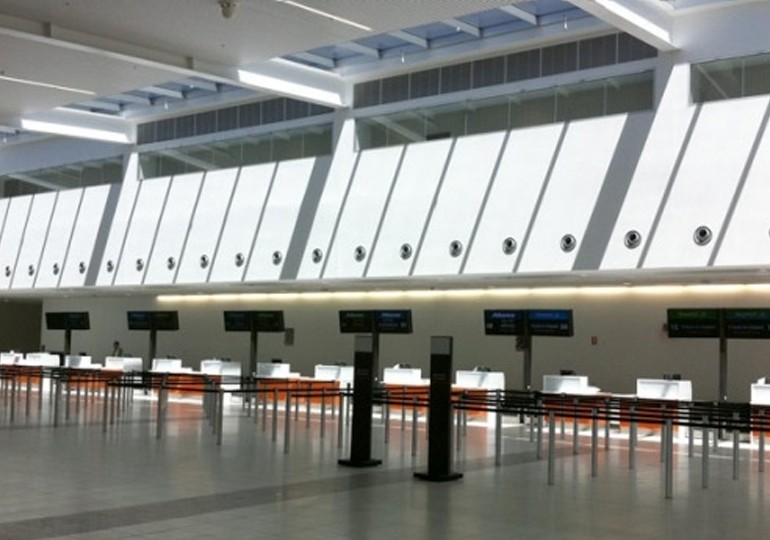
This terminal was designed specifically for domestic air travelers for the fly in-out workers, utilizing a state of the art conveyor baggage system, catering for high volumes of traffic.The fire sprinkler system is throughout terminal complex (Ordinary Hazard 1, 2 & 3 categories), all feed from an underground ring main system provided by the site plumber. The terminal has 2 off FM200 fire suppression systems protecting sensitive electrical equipment.The terminal fire sprinkler system has pressure reducing installed downstream of the fire sprinkler control at various pressure settings depending on the hazard classification & flow and pressure requirements determined by full hydraulic calculations.
The conveyor baggage handling system on this projects was mainly suspended by suspension rods from the roof structure (leaving the majority of the floor area clear). The fire protection was ran under the conveyors, directly fixed to the conveyor supporting structure, and the piping was modularized into 3m & 4m lengths of piping to make manufacture simpler and construction on site easier.After the contract completion and DKFD involvement was finished, on the Terminals WA project at the clients consultant's request the fire contractor was instructed to remove the pressure reducing valves were removed and replaced with orifice plates (size based on the full hydraulic calculations). This we understand was due to a site issue of the pressure reducing allowing flow and triggering the alarms.The introduction orifice plate in lieu of pressure reducing valves may create issues;-
- Excessive pressure in the sprinkler system 1300 kpa (when the fire pumps & system jockey pump are operating at zero flow, 1300 kpa is the pump churning pressure), where in AS2118 that maximum pressure on a sprinkler is limited to 1000 kpa.
- May be unable to achieve the 3.0 minute fire alarm activation from the direct brigade alarm (DBA pressure switch) test from the remote test valve location.
- In event of a fire larger than the designed area for particular hazard classification, the orifice plate will restrict the flow of water, and therefore the fire brigade cannot boost system flows for any additional flow requirements for a larger fire scenario.
Perth International Airport Terminal T1 Expansion
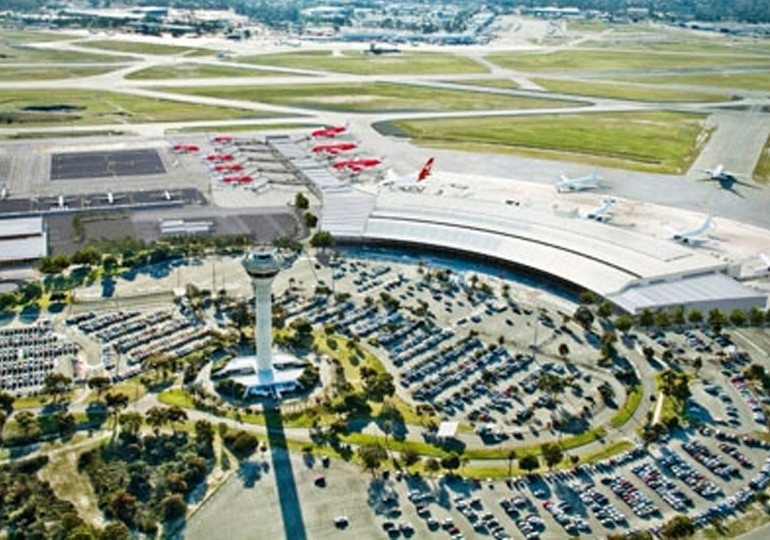
This is an existing T1 Terminal that has been extended. The existing terminal was designed pre-CAD and all the available drawings are hand drawn. The new terminal extension is in some parts 2D AutoCAD and some trades (structural and air conditioning) were drawn in 3D Revit & all the co-ordination done by the builder used 3D Navis.All the consulting & architectural drawings were all drawn in 2D CAD. The contractors majority of the fire services drawings were drawn in 2D, with some smaller node areas drawn using Revit
The principle of 3D CAD drawings all being overlayed and co-ordinated is a good idea, but everything needs to be in 3D. Creating working drawings in 3D (AutoCAD or Revit) is time consuming and more expensive design
phase, but the merits in co-ordination of various trades is very beneficial.All the water supplies are connected to the Co-Generation fire pump utilizing the existing + new underground fire ring main, and connected in the new terminal & pier area rings mains, the new ring main system can provide the desired flow and pressure for the existing terminal & new extension areas.On this project pressure reducing valve are also used to limit the sprinkler system operating, thus conserving water supplies. The project consultants (same as the Terminals WA project), required the pressure reducing valves to be downstream of the fire sprinkler alarm valves.At the time of this web site post the project was still in construction phase, and the pressure reducing valves operations were untested.Perth International Airport artist impressionAdjacent is an artist impression fo the finished Terminal in the foreground left, and in the background left bottom is the Terminal WA for flyin-flyout workers
Perth International Airport artist impression
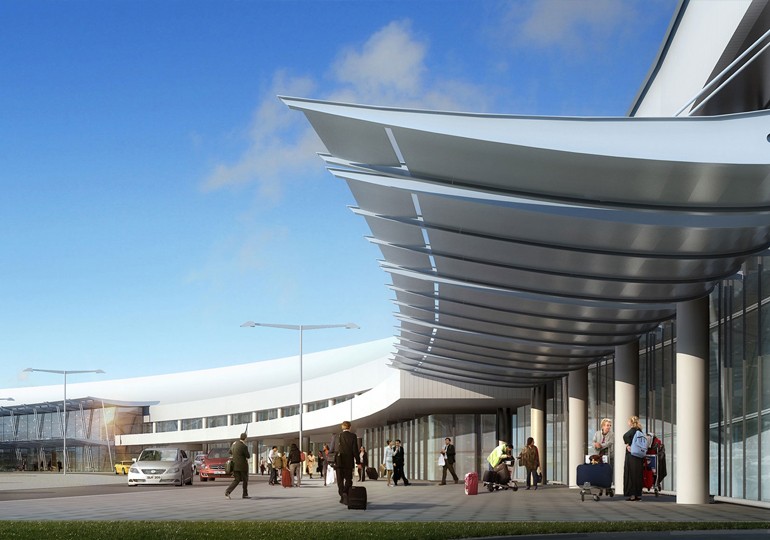
Perth International Airport night front view
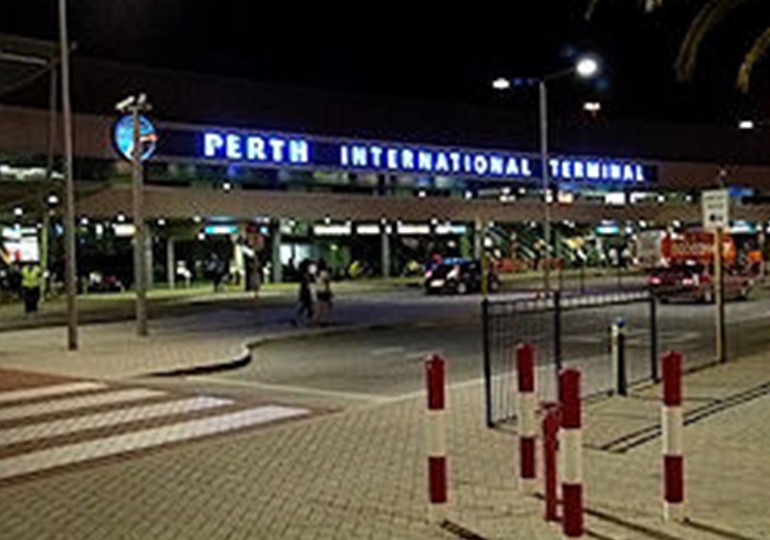
Myers Forest Chase, Perth WA
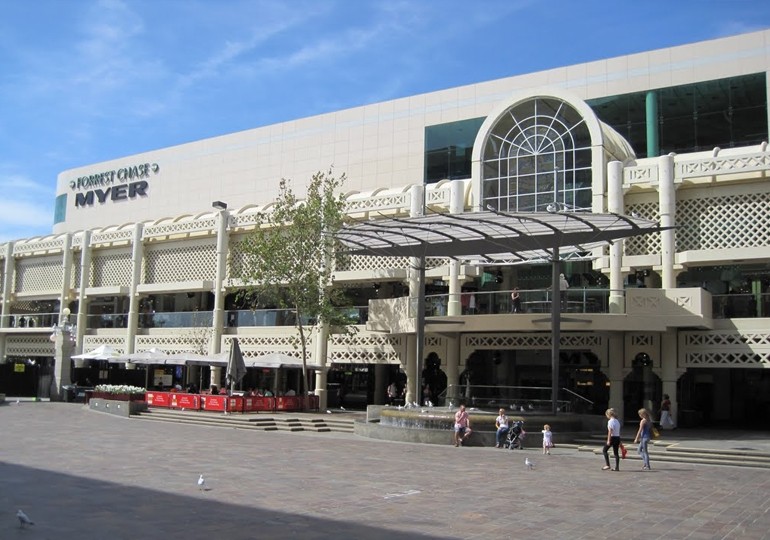
This project was pre-CAD & hand drawn, and designed for the selling areas to be ordinary hazard group 3 classification. During the early design and construction stages, the fire contractor (then Wormalds (now TYco)), were instructed by the builder and project consultant to design the fire sprinkler system below ceiling head layout on an open area layout, with fire sprinkler heads a maximum spacing's.After the fire piping was roughed in, and pressure tested (air firstly and then water) prior to below ceiling head fit out, Myers produce a revised set of reflected ceiling plans, having numerous new walls and bulkheads and lowered ceiling areas. We then site welded hundreds of DN50 plugged outlets along the fire mains, to give the fire contractor the ability to feed
the many new additional below ceiling heads. All of the new pipework was designed and site manufactured & fitted to accommodate the revised ceiling & below ceiling head located by the onsite fire system designer (Darryl Knapp) and the fitters leading hand, using hand sketches and later the information was transferred on the as built drawings. This was a variation to contract, based on the original schedule of rates, and the project was still completed on schedule.The water supply for this project was grade 1, directly pumped from the town's mains supplies connections from Wellington & Hay streets water supply mains.
Melbourne Concert Hall & Theature & Spires Building, Melbourne VIC
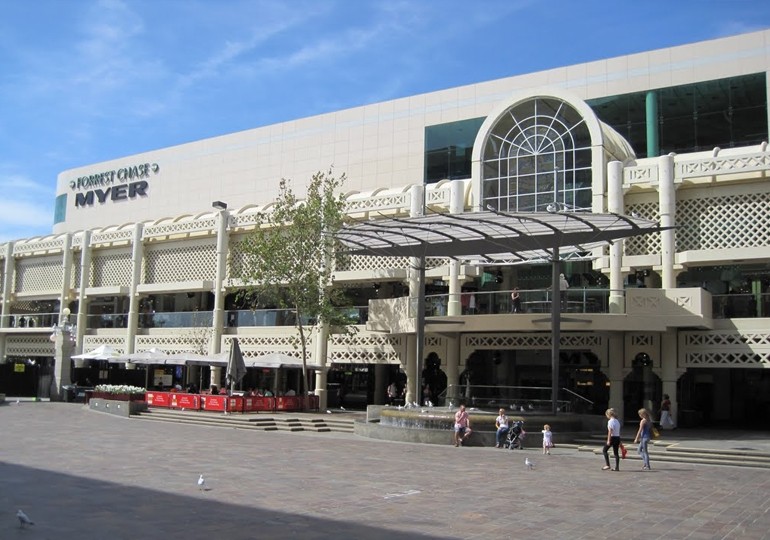
Concert Hall
The Concert Hall is in the foreground (bluish Colour) and the Theature& Spires Building is in the background.The Concert Hall project was pre-CAD, all hand drawn. The project based on circular design methodology of the Concert Hall. All corridors and walls were all curving following various radius as set out by the project architect.To fit piping to a circular building is very difficult, all the pipe deflections to follow the building curves were individually hand calculated to get the correct angles. The set out of the site were fitters was also difficult, where we gave dimensions off wall at each change of direction point, and then string lining between point to get the pipe routes.
This was achievable for the piping system rough in phase, and we attempted to get the ranges and below ceiling head feeds within 300mm of the final locations. As there were no straight walls to measure from, everything was set out using string lines at right angles to the fire mains. Mostly we achieved our goals, getting the below ceiling heads feed near the final architectural points.The ceiling over the main concert hall area was another challenge, firstly very high above the floor level, massive trusses spanning the complex all covered in fire retardant spray that could not be damaged. The piping deign was ran at roof level under the roof z purlins, but the installation was very difficult due to the height and tiered floor for the seating. We utilized builder supplied scaffolding for the final ceiling structure and used scaffolding above this platform to fit all the piping and droppers to feed the below ceiling heads. Naturally in the roof void were all the normal trades (AC ducting / lighting / power / plumbing) that had to be coordinated with.Water supply was taken for the towns main supplies, and boosted with fire booster pump to achieve the required flow and pressure for the project fire design requirements.The final finished project was achieved, there were many issues relating to piping & below ceiling head locations, to achieve the architects drawn reflected ceiling plans. Seeing the final finished job, it looks amazing, and we believe that the architectural project goals were achieved.
Theature & Spires Building
The building is a more conventional design, and has a large seating autotrium with a very large stage area. This building was built at the same time as the concert hall (pre CAD all hand drawn), still a complex design. Water supply was taken for the towns main supplies, and boosted with fire booster pump to achieve the required flow and pressure for the project fire design requirements
Hamersley Iron Switch Rooms CO2 Fire Suppression system & Various Fire Sprinkler Systems to Buildings and Conveyors , Tom Price WA
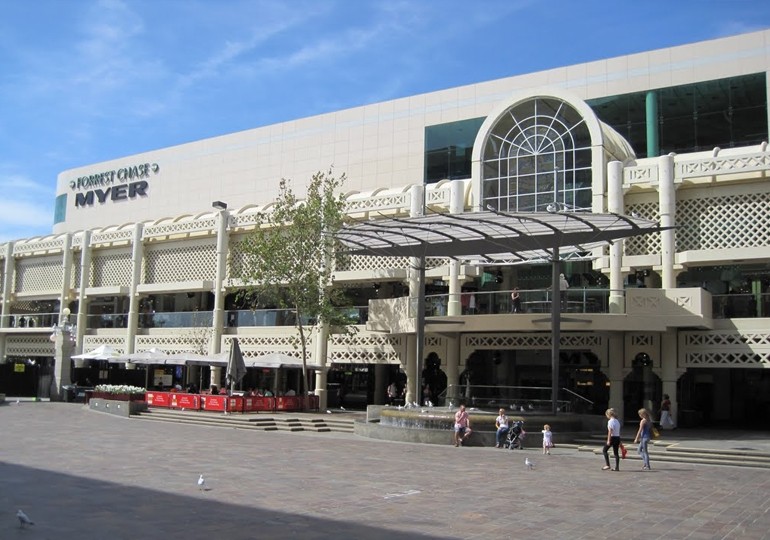
Main Switch Room
This project was pre-CAD, and all hand drawn. There was an electrical switch room that under the insurer Factory Mutual Global (FMG) require CO2 total flooding fire suppression system (33% concentration) to FMG codes to the switch room area, for one of Hamersley Irons vital facilitiesThe was a requirement for an initial and reserve banks of cylinder, approx. 90 off high pressure 102 lb capacity cylinders in each bank, all fully connected by piping to the risk and controlled by an electrical detection system consisting of smoke and thermal systems + VESDA smoke detection system to all cabinets.As the vast amount of gas was forced into the risk, the
natural air has to be vented, this was achieved by many barometric damper position at high level to let the natural air our allowing the CO2 gas to fill up from floor level upThe project insurer FMG required a full discharge test, proving the required CO2 concentrations were achieve, this was carried out successfully.The project safety officers wanted to see in an event of a CO2 system activation, what happens in the risk, so they suited up with fully self-contained breathing apparatus, and positioned themselves around the risk to watch the system operation first hand.We have an CO2 concentration gas analyzer device/meter positioned outside the risk, with 3 separate channels to monitor the CO2 concentrations at 3 different levels as required by FMG, all recording the from the initial system activation to 30 minutes post system operation.The test went like clockwork, and we successfully maintained the required concentrations, all the safety officer emerged from the room with many stories on what happened inside the risk during the initial system operation time & post soak time.The initial bank of expended cylinder were removed after the successful test completion, and returned to Perth for refilling and back to site for installation, the reserve bank was used during the time the initial bank of cylinders were refilled & refitted & recommissioned.To my knowledge the system is still operation, and has never been a fire scenario in this facility. This was one of the biggest CO2 system tested by myself, and we were nervous that the system would operate as designed, but all was good on the day!
Fire Sprinkler / Hydrant / Hosereel / Deluge Systems
There are many fire sprinkler system on this site, protecting the administration building, warehouses, Ampho shed, conveyors, power generation facility (fire water deluge systems on each diesel generation engines & fire sprinklers on the engines cooling towers), refining plant & many other facilities all to Factory Mutual (FMG) standards.There are also various fire hydrant system & fire hydrant dry risers + fire hose reel system + fire extinguishers, to various structures around the site all compliant to Factory Mutual (FMG) requirements.There is a fire deluge system to the main workshop floor pit area under where the haul packs (very large trucks) are serviced and repaired.All of these systems were design and drafted in pre-CAD time, so all the drawings were hand drawn. All of the building / structure / conveyor systems on this site only have hand drawn drawings, and in many cases the only way to complete the design was to site measure the structure and create new drawings of the project so the design could be completed.------------------------------------------------------------------------------------------With our vast experience in numerous projects & fire protection system type (main projects are listed under the "Project List" tab), there are many aspects to fire protection design, depending on the following key points, which then gives us a basis of the overall system design;-
- Project classification based on client requirements and statutory codes
- Applicable fire codes - Building code of Australia, Australian Standards, Factory Mutual Globe (FMG), National Fire Protection Codes (NFPA), Euro codes, ect.
- Fire Hazard classification, based on the Australian Standards or applicable Fire Codes (i.e. Factory Mutual (FMG) / National Fire Protection Association (NFPA)
- Type of fire protection, wet type fire sprinkler, pre-action fire sprinkler, dry-fire sprinkler, deluge water spray, low / medium / high velocity water spray, gaseous fire protection systems, foam systems (low / medium / high expansion systems), water cannons, fire hydrant and hose reels, extinguishers, electrical detection systems (smoke detectors, heat detectors, liner heat detection, aspirated smoke detection, Evacuation Warning systems), plus many more types.
- Available water supply sources (towns main, Fire Water Tanks, Bore, Lake / River?)
- Fire brigade connections facilities for fire sprinkler systems (location / type / configuration)
- Fire Brigade & site monitoring
Once these key points are known, then we can proceed with the fire protections design (either Consultancy or construction) to suit the client requirements, insurers and the statutorily requirements.We hope that the above give you some idea of the simple and very complex design that need to be carried out, to achieve the fire protection requirements, and queries, please contact us by email on admin@dknappfiredesign.com.au